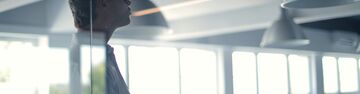
Opleidingen
Lean Black Belt in Manufacturing
Lean Manufacturing kreeg wereldwijd bekendheid dankzij de bestseller 'The machine that changed the world', waarin de succesfactoren van het Toyota productiesysteem beschreven werden.
Waarom dit thema?
Het Lean Manufacturing concept is het vervolg op het massaproductiesysteem zoals dat in de jaren twintig bekend werd door Ford. Lean Manufacturing is na de Tweede Wereldoorlog ontwikkeld door Taiichi Ohno en Eiji Toyoda van automobielfabrikant Toyota in Japan.
Lean Manufacturing kreeg wereldwijd bekendheid dankzij de bestseller 'The machine that changed the world', waarin de succesfactoren van het Toyota productiesysteem beschreven werden.
In de jaren tachtig heeft Lean Manufacturing ook in Amerika voet aan grond gekregen. Dit werd mede veroorzaakt door de samenwerking tussen Toyota en General Motors, die samen een fabriek bouwden. Het heeft tot het eind van de jaren tachtig en het begin van de jaren negentig geduurd, alvorens Amerikaanse bedrijven zelf ook zogenaamde 'Lean Manufacturers' wilden worden.
Vandaag past elke organisatie wel een systeem toe om de productiviteit te verhogen, de doorlooptijden te verkleinen en om in het algemeen de kosten beduidend te drukken.
Lean werkt:
- Focus op toegevoegde waarde voor uw klant
- Maak dus verspillingen zichtbaar
- Optimaliseer dan uw productie
- Word zo meer concurrentieel!
Waarom deze opleiding?
Deze opleiding biedt een sterk lessenpakket aan met voldoende variatie tussen theorie en praktijk. De docenten slagen er telkens opnieuw in de cursisten te boeien en bruikbare tips&tricks aan te reiken vanuit hun eigen ervaringen.
De nieuwe evoluties naar QRM en Polca tonen aan hoe deze opleiding steeds mee evolueert met de markttrend, waarin flexibiliteit, variatie en snelheid cruciaal zijn.
U leert tijdens deze cursus:
- hoe u binnen uw organisatie voortdurend op zoek kan gaan naar processen die geen toegevoegde waarde creëeren
- hoe u uw productieprocessen in kaart kan brengen
- hoe u binnen de productie-afdeling aanzienlijke kosten kan besparen
- hoe u zo weinig mogelijk afwijkingen op uw productieprocessen kan nastreven
- hoe u uw omsteltijden kan reduceren
- hoe u orde en netheid kan behouden binnen uw productie-omgeving
- hoe u via de juiste coachings-vaardigheden al het vorige kan ondersteunen als manager
- ...
Houdt er rekening mee dat u tijdens de opleiding af en toe een opdracht meekrijgt of materiaal uit uw werkomgeving dient mee te brengen.
Inhoud
Deze opleiding is deels modulair opgebouwd zodat u -indien gewenst- een pakket kan samenstellen dat aan uw specifieke behoeften beantwoordt. U kan dus bepaalde modules afzonderlijk volgen. We raden echter wel aan om de volledige opleiding te volgen, omdat u door de geïntegreerde totaalbenadering immers de beste resultaten zal behalen. Bovendien is de kost per module dan veel lager.
Dit is het programma van de 14-daagse opleiding. Voor modules die apart gevolgd kunnen worden, kan u inschrijven via de opgegeven links.
Module 1A: Lean Manufacturing & intro in the human factor (1 dag)
(apart inschrijven kan, zie ook: Lean Manufacturing & intro in the human factor)
- Wat is Lean Manufacturing ?
- Geschiedenis van Lean
- Bouwstenen van Lean Manufacturing
- Principes en methodiek van Lean Manufacturing
- Link met de ‘mens'
- De 7(+1) verliezen
- Hoshin Kanri
- Lean assessment
- Overzicht van de belangrijkste technieken binnen Lean Manufacturing
- 5S voor orde en netheid
- Value Stream Mapping
- Total Productive Maintenance (TPM)
- Overall Equipment Effectiveness (OEE)
- Single Minute Exchange of Die (SMED)
- Visueel management
- Poka Yoke
- De Gemba-Manager
- De Gemba-Manager?
- Keer de driehoek om
- Kenmerken van een Gemba-Manager
- Ga kijken
- Toon betrokkenheid
Module 1B: Kata coaching (1 dag)
(apart inschrijven kan, zie ook: Kata Coaching - aparte editie)
- Wat is de verbeter-kata?
- Begrijp de richting
- Wat is een visie?
- Wat is een uitdaging?
- Value Stream Mapping als middel om richting/uitdaging te bepalen
- Begrijp de huidige toestand
- Klantvraag en huidige cyclustijd
- Kenmerken van het huidige proces
- Machinecapaciteit
- Benodigd aantal operatoren
- Resultaatmetingen
- Leg de volgende doeltoestand vast
- Stappen om een doeltoestand vast te leggen
- Parkeerplaats obstakels
- Beweeg richting doeltoestand met PDCA en coaching cycli
- PDCA-cycli richting doeltoestand
- De 5 coaching kata-vragen
- Begrijp de richting
Module 2: Value stream mapping in manufacturing (2 dagen)
(apart inschrijven kan, zie ook: Value stream mapping in manufacturing)
- Situeren van 'process mapping' - basisprincipes, regels, symbolen en stappen
- In kaart brengen van de bedrijfsprocessen
- Situering van 'value stream mapping' - basisprincipes, methodologie en symbolen
- In kaart brengen van de startsituatie: current state
- Stappenplan om van de 'current state' de 'future state' te bepalen
- Case
Projectselectie
Tussen module 2 en module 3 voorzien we een moment per cursist om tot een gedegen projectselectie te komen in het kader van het te maken eindwerk
Module 3: Lean-technieken in manufacturing (7 dagen)
Module 3A: Lean in de praktijk, met Lean Game (1 dag)
- In dit Lean Game wordt een omgeving gecreëerd om een reële situatie te simuleren. Hierdoor kan zeer gericht de juiste techniek gekoppeld worden aan de juiste problematiek in een productieproces. ‘Learning by doing' is hier het trefwoord.
- In de volgende modules kan dan op een gepaste manier dieper worden ingegaan op de diverse technieken.
Module 3B: 5S-methodologie in manufacturing (1 dag)
(apart inschrijven kan, zie ook: 5S in manufacturing - eventueel aparte editie)
- 5S: de Japanse filosofie die uw bedrijf op weg helpt naar wereldklasse
- 5S: implementatie
- Praktijkgetuigenis + bedrijfsbezoek: 5S bij Atlas Copco
Module 3C: Total Productive Maintenance (TPM) (1 dag)
(apart inschrijven kan, zie ook: Total Productive Maintenance)
- De productie- en onderhoudsfunctie
- Wat is TPM?
- Verliezen en installatie-effectiviteit
- Verschillende vormen van onderhoud
- Verbeteren door TPM
Module 3D en 3E : Overall Equipment Effectiveness (OEE) en Single Minute Exchange Of Die (SMED-omsteltijdreductie) (1dag)
Overall Equipment Effectiveness
- Verliezen m.b.t. de machines en installatie-effectiviteit (OEE)
- O.E.E. als 'key performance indicator'
- Hoe een O.E.E.-project plannen en implementeren?
- Hoe de O.E.E.-waarden analyseren?
- Welke zijn mogelijke verbetermethodieken binnen het O.E.E.-gebeuren?
Single Minute Exchange Of Die
- Inleiding SMED
- De SMED-methodiek
- SMED-hulpmiddelen
- Praktische SMED-toepassing
Module 3F: Visueel management en poka yoke(1 dag)
Module 3H: Lean in de praktijk, met Lean Game - aan de slag, met o.a. technieken voor productiviteitsoptimalisatie in manufacturing (1 dag)
- Met de opgedane kennis en vaardigheid van Lean-technieken kan vanaf nu op een zeer praktische manier aan productiviteitsverbetering gedacht worden in de context van 'Lean Manufacturing'. Hiervoor gebruiken we hetzelfde Lean game als in module 3A.
- Het ontwerpen van productieprocessen die flow ondersteunen:
- Analyseren van werkmethodes en het kwantificeren van de verschillende vormen van 'waste' in werkmethodes
- Cel- en werkplek layout
- Balancering voor one piece flow
- Ontwerp en implementatie van pull/kanban systemen
- Basisprincipes
- Implementatievormen van pull-systemen
- Hands-on simulatie oefening QRM (Quick Response Manufacturing)
Module 4: Lean verbetertechnieken (1 dag)
- Hoe verbeteren vanuit een 'lean-standpunt'?
- Van PDCA (Plan, Do, Check, Action) naar een 7-stappenplan
- Enkele specifieke kwaliteitstechnieken
- Wat betekent 'sigma' en 'six sigma'?
- Six sigma: aanpak
- Differentiëring van six sigma tegenover andere kwaliteitsbenaderingen
- Case studie
Afsluitende opdracht (1 dag)
Voor wie
- plant- en operation managers
- productiedirecteurs
- productieverantwoordelijken
- quality managers en engineers
- maintenance managers
- leidinggevenden en beslissingsnemers uit een productieomgeving
- ...
Attest vs certificaat
Het certificaat 'Lean Black Belt in Manufacturing' wordt toegekend aan kandidaten die slagen in de individuele opdracht.
Deze individuele opdracht bestaat uit het uitwerken van een 'verbeteringsopdracht' binnen een bestaand proces van uw productie-afdeling. Op het einde van de opleiding, stelt u aan de hand van een presentatie uw 'verbeteringsopdracht' voor aan de jury en andere deelnemers.
Indien u verkiest om geen individuele opdracht uit te werken maar toch alle lessen heeft bijgewoond, krijgt u een attest van deelname.
Cursisten aan het woord
Ik heb de opleiding gevolgd om de rol van TPM in LEAN beter te leren begrijpen. Doordat ik nu dit groter beeld zie kan ik in mijn rol als TPM'er de organisaties waarvoor ik werk beter begeleiden. dankzij, niet alleen kennis, maar ook heel veel praktische ervaring heb ik veel bruikbare tips en voorbeelden van de lesgevers meegekregen. Bedankt docenten, bedankt Amelior! Een aanrader voor iedereen die zich in de kunst van Manufacturing wilt verdiepen!
Jan NOTE - NOVETECH BVBA
Ben heel blij de opleiding gevolgd te hebben. Ik heb heel veel opgestoken van de lesgevers en ook van de mede-cursisten!
Stefan POLFLIET - DESLEE CLAMA NV
Heel interessante en praktisch bruikbare cursus, die je direct in de praktijk kan omzetten!
Steven VANDENBULCKE- A&S ENERGIE nv
Ik heb het gevoel dat mijn persoonlijke toolbox nu beter gevuld is om mijn bedrijf te helpen verbeteren en competitiever te maken!
Nicolai DIELTIENS - LANXESS RUBBER NV
De cursus Lean Manufacturing laat vele mogelijkheden zien waar Lean tools kunnen toegepast worden, zo kunnen Lean Tools helpen in een verbeterde organisatie structuur van Labo's en Documentatie Tools.
Jan VERREYT - BP CHEMBEL
De docenten van Lean Manufacturing Expert hebben ruime ervaring in de bedrijfswereld en delen die met de cursisten. Ook tussen docenten en deelnemers is er ruimte voor gedachtenuitwisseling. Dat is prima, want zo kom je tot reflectie over de eigen organisatie en die heb je nodig om lean te doen slagen. De opleiding heeft mij doen inzien dat je door de noden en de wensen van de klant te begrijpen, een omgeving kan creëren waarin er gefocust wordt op het elimineren van de verschillende soorten verspilling ('waste'). Daarbij moet wel de nodige verantwoordelijkheid aan de vloer (en ondersteunende diensten) gegeven worden, zodat dezelfde mindset over de hele organisatie heerst. Iedereen van hoog tot laag moet echt gaan vertrouwen in het continu verbeteren van de organisatie. De Human factor (empowerment en betrokkenheid) is dan ook een leidraad doorheen de cursus. Tijdens de cursus worden de Lean tools (en hun specifiek gebruik in verschillende situaties) goed uitgelegd. Het Lean game vond ik een topper en het bedrijfsbezoek (Amcor) een pluspunt voor je eigen latere uitwerking en implementatie op de vloer. Voor mij is dit duidelijk: lean werkt! Door lean projecten kunnen we onze jaarlijkse groei opvangen zonder te investeren in resources en uitbreiding van faciliteiten.
Dennis VAN HAEKEN - Terumo Europe
Lean heeft mij doen inzien dat een product niet enkel bestaat uit de onderdelen die er aan vast hangen. Door het toepassen van de verschillende technieken (bv. Value stream map) komt men in aanraking met de verschillende departementen (logistiek, productie, administratie, ...) binnen een bedrijf en krijgt men een beeld van wat er nodig is om een product tot stand te brengen. Vaak gaat dit gepaard met verliezen binnen de organisatie die nauwelijks of niet zichtbaar zijn, omdat ze door de jaren heen zo ingeburgerd zijn dat ze als 'normaal' bestempeld worden. Lean heeft mij doen inzien dat ook deze verliezen moeten worden aangepakt om een organisatie zo optimaal mogelijk te laten renderen en zo de concurrentie een stap voor te blijven.
Benny DE JONG - BRABANTIA S&L Belgium
Wij met ons bedrijf zijn ervan overtuigd dat de Lean filosofie, de enige juiste manier is om te overleven in deze harde concurrentiële wereld. Daarom was er interesse van mijn persoon om deze opleiding te volgen, wat mij heel erg bevallen is. Ik loop door ons bedrijf met een heel andere benadering van de feiten.
Davy VANDEWALLE - WINSOL
De opleiding heeft binnen onze organisatie gezorgd voor een extra stimulans bij invoering van gestructureerde verbeterplannen. We zijn aan het denken gezet over de plaats van ‘Lean' binnen de totale verbeteraanpak en hebben onze totale benadering op papier gezet en besproken binnen het management. Nu gaan we deze Q-approach bespreken met het middenkader om vervolgens met prioriteiten per afdeling aan de slag te gaan. Ondertussen zijn we bezig onszelf de technieken eigen te maken en dit onderdeel te maken van ons opleidingsplan. Kortom, voor Voestalpine Polynorm Van Niftrik kwam deze opleiding op het juiste moment en gaf het voldoende houvast voor een nieuwe stap naar continuous improvement.
Gert TRAA - VOESTALPINE POLYNORM VAN NIFTRIK
Ik vind het een zeer leerzame cursus, waarmee ik in de praktijk vrij snel aan de slag kan. Sommige modules vragen wel om meer uitdieping en zelfstudie omdat deze in het korte tijdsbestek onmogelijk volledig aan bod konden komen.
Stefan KEMPENEERS - THERMO CLEAN
Meer en meer groeit de interesse voor procesmanagement technieken in de non-profit sector. Deze uit de industrie afkomstige methodiek kan gemakkelijk vertaald worden naar de gezondheidssector en heeft mij als kwaliteitscoördinator van een ziekenhuis veel bruikbare informatie opgeleverd. Door toepassing van 'Lean principes' aangeleerd in deze cursus werden reeds enkele projecten succesvol afgesloten en dit zowel in de ondersteunende als in het zorgdepartement van het ziekenhuis. Tevens werd het kwaliteitsmanagement in onze instelling verder geoptimaliseerd dankzij deze opleiding. Beslist een aanrader voor iedereen die wenst de kwaliteit en de efficiëntie in zijn organisatie te verhogen.
Peter OSTEN- BELGISCH ZEE-INSTITUUT VOOR ORTHOPEDIE
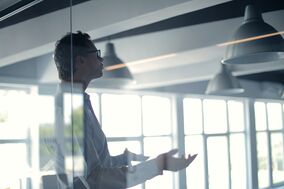